Manage Delivery Schedules For Multiple Sales Orders In D365
Delivery Schedules | Delivery Planning | Dynamics 365
In almost every project you have worked on, you might have encountered a crucial requirement for handling schedule deliveries on purchase/sales orders or even blanket order types. Previously, Dynamics allowed users to select their order type as Blanket order when creating both sale and purchase orders. However, after the update in 2012 AX, they can no longer go with blanket orders.
Somewhat, you can just create a few lines on the order grid and adjust the delivery date for each; sounds easy, right? Well, you would be pretty much on the point, except for a few things.
First, the obvious thing, it’s a manual entry. For firms going through thousands of orders with enormous scheduled deliveries, it’s a tedious process while not ignoring the human errors that it would accompany. And let’s not discuss the horrors a manual entry would bring when one of your customer representatives is on the call with the client while putting those entries, evidently, why a customer would wait long enough for entering the complete order details.
Additional exposure to scheduled deliveries is the ease of managing discounts and pricing. There were several cases where the firm offered volume-based discounts, but customers faced stunned deliveries for months instead. This was due to placing the complete order for an extended period to receive discounts at once. In addition, putting deliveries as single-line discounts will result in rejected line discounts. The user then would have to enter the value on every line manually.
Business is all about reducing the lead time. That is making the complete process as short as it could get. And manual entries don’t help much in this sector. There’s a probable chance that you might have already known about creating scheduled deliveries in Dynamics 365; however, for those of you who aren’t sure about the procedure, you can jump to the fourth part of this blog and kill your curiosity right away. For the rest staying with the fellow, there is some staggering insight for delivery schedules.
Plan a Better Delivery Schedule
Considering on-time delivery comes with the betterment of transportation management. In it, businesses calculate their time spent per delivery, keep operations on track, and try their very best to reduce wait time.
Scheduling is the act of making preparations for multiple deliveries with several locations, routes, and drivers to achieve tasks and customer satisfaction. To some extent, it requires a purely logical approach against time management with a thorough understanding of factors impacting modes of delivery operations.
Theoretically, scheduling deliveries is more of an art, as it is discipline. However, when done efficiently, good scheduling can help you in many ways. It enables you to develop an understanding of what your business can achieve realistically within a specified time span. Further, scheduling adds contingency time if something unexpected occurs during the life cycle.
Scheduled deliveries allow drivers and agents to apply for all the perks mentioned in their work agreements. Scheduling logistics management will also help in avoiding additional orders that your operation line can’t handle. Apart from that, scheduled deliveries can help you to;
- Make sure you have adequate time to attend to each customer and maintain a high level of service (even if delivery is due by the end of the day).
- Provide all perks to drivers and delivery agents following their labor agreements.
- Implement delivery techniques to expand your operations and meet the organization’s long-term goals.
Many businesses fail to recognize that time is a finite resource. It’s the only one you can’t sell or buy. But it’s the one we waste the most or use ineffectively. That is why delivery dates are so crucial. They assist you in keeping your operations on track as you work toward both short- and long-term objectives. That was all for binding a better delivery schedule plan. Now let’s go to the part where we’ll know about the factors having a considerable impact on your on-time delivery time.
SUMMARY
Scheduled deliveries via effective transportation planning can streamline your supply chain, making it more efficient than ever. Several factors play their role while you are in pursuit of scheduled deliveries by giving several advantages to services, labor, and expanding operations.
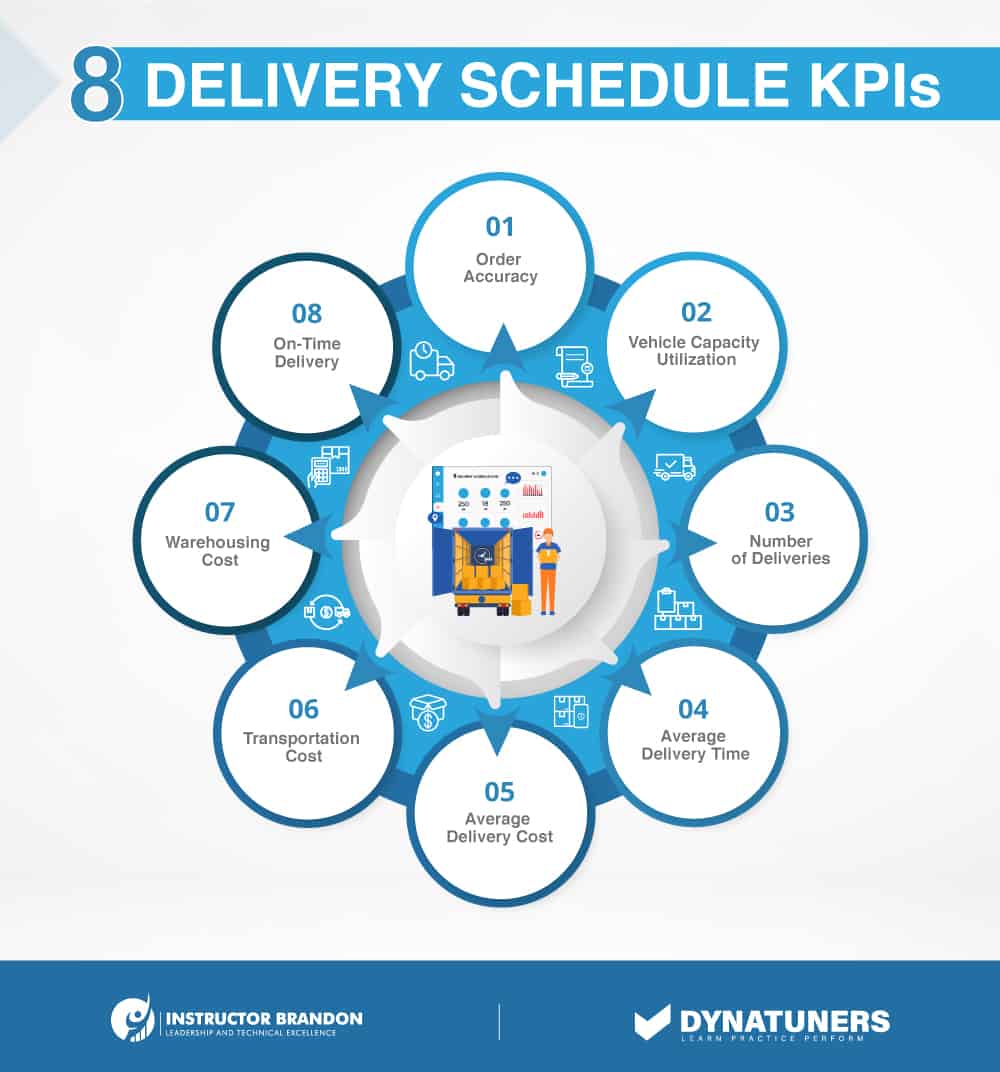
Factors affecting Scheduled Deliveries
Achieving excellence in scheduled delivery is a way to improve manufacturing productivity, increase the finished goods output and streamline operations. Businesses need to understand the factors affecting deliveries planned in order to optimize processes. Here are five common elements having massive effects on your delivery schedules.
Unexpected Stockouts
Stockouts are bad for manufacturers since they make it hard to produce things if they lack the necessary parts and inventory stock to finish the job. This not only results in poor delivery schedule templates and disgruntled consumers, but it also generates bottlenecks and missed time, both of which cost money to the company. In the worst-case scenario, it could result in lost sales and consumers if they choose to shop elsewhere for their merchandise.
You can avoid stockouts by managing the procurement and delivery of manufacturing components based on usage, automating your inventory procedures with Dynamics 365, and applying Just in Time (JIT) inventory control.
Variability in lead-time
Because lead times differ from supplier to supplier, estimating when all of the essential distribution of products will take place isn’t easy. As a result, it’s more difficult to manage production. Consolidating your suppliers is an efficient strategy to eliminate this problem and ensure that everything needed for manufacturing arrives simultaneously. This can save money on shipping and make schedule planning much more manageable.
Shipment delays
Factors affecting deliveries include raw material shortages, natural disasters, and human error; perhaps the most unexpected and challenging to regulate. However, by finding suppliers close to your business or working with a supplier who keeps goods on hand while constantly monitoring usage, you can minimize the chance of delivery delays. Furthermore, the fewer incoming shipments you have, the less likely you will experience order fulfillment delays.
Unwanted Processes
When you build each component of a finished assembly, each order takes longer to complete, lowering output and return on investment. To save on production hours, managers can use outsourcing sub-assembly activities to optimize the process. As a result, product distribution will take less time to complete, achieve delivery excellence, and eventually increase customer satisfaction and profitability.
Inefficient inventory
Scheduled deliveries can be harmed if your inventory or transportation management system is out of control. Improving inventory control ensures that you know exactly what and how much inventory stock you have on hand, ensuring that you have all the components you need for manufacturing runs. Effective inventory control will lower inventory expenses, reduce handling costs, and improve production processes.
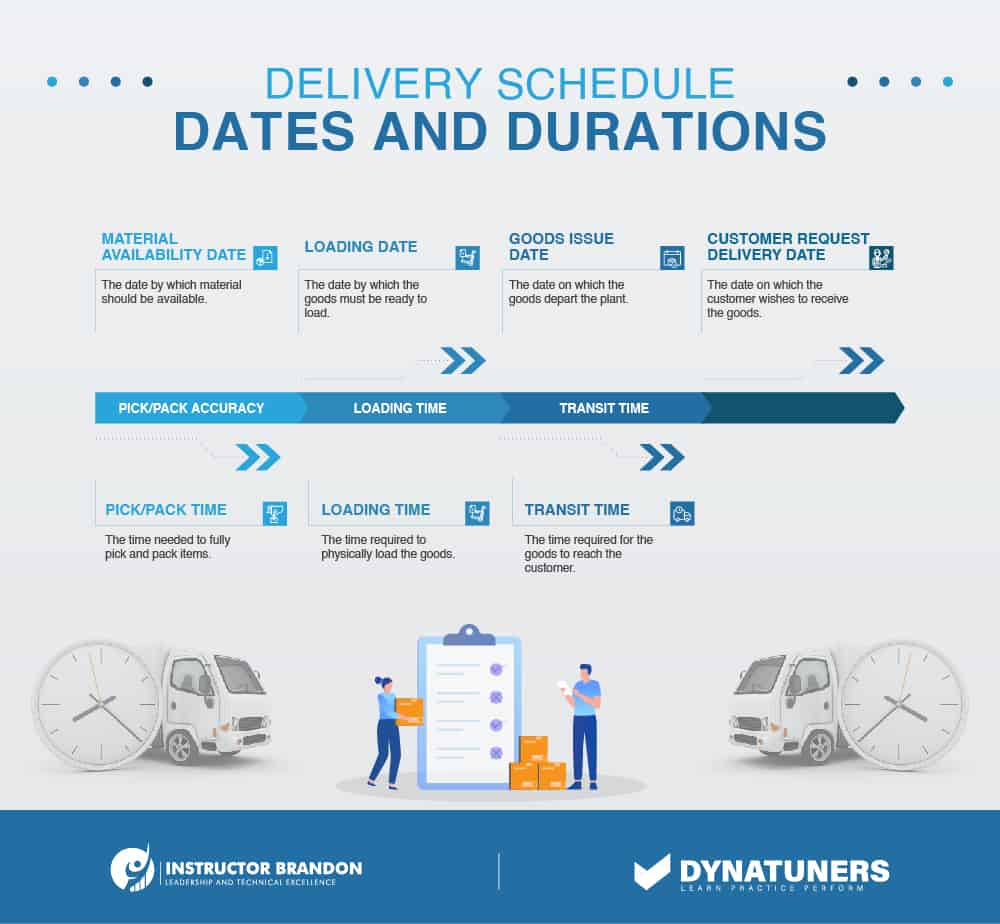
SUMMARY
External factors can affect item manufacturing receipted into your warehouse management, in addition to the above five factors determining delivery schedules. For example, if you don’t have a JIT arrangement or standing order of the same inventory stock in the exact amounts with your suppliers, a significant portion of the lead time can be consumed by how busy that supplier is and the number of total orders ahead of yours.
How does Dynamics 365 help in Delivery Planning?
Businesses use Dynamics 365 to discover the best cost-effective routes given their limits. However, when it comes to establishing optimal timetables and paths, the appropriate solution can help organizations save time, cut expenses, and boost production by combining real-time and historical data.
Here are some examples of how Dynamics 365 operations and supply chain management can assist you:
Digitized route planning
With ease, Dynamics 365 can determine the most cost-effective routes by factoring in numerous constraints. Set your limitations, parameters, logistics service time estimates, and other criteria, then let a robust AI-powered platform handle the rest. Sure, you’ll have to make minor changes to the plan, but it’ll take a fraction of the time. Most importantly, the machine will forecast ETAs far more precisely than a human planner could.
Real-time monitoring
Fleet managers who can readily track drivers’ whereabouts and activity in real-time have a better handle on their operations. In addition, real-time monitoring and visibility allow fleet managers and dispatchers to see disruptions and exceptions as they occur and take proactive efforts to address them.
Efficient channel for communication
Internal teams can interact more efficiently and effectively with the delivery planning assistance of Dynamics 365, mainly when it includes an easy-to-use driver mobile app. For example, dispatchers and fleet managers can send drivers their daily job assignments, route plans and sequences, and other instructions or updates via Dynamics 365 mobile app. In contrast, dispatchers can automatically communicate with consumers about delivery timetables. Moreover, delivery personnel can collect electronic proof of delivery via time-stamped signatures, pictures, videos, and notes.
Now we proceed with the long-waited part of the blog, creating delivery schedules.
Master Production Schedule | |||||||||||
Order Status | Production Number | Customer | Product List | Variation | Total Production Quantity | Starting Inventory | Ending Inventory | Start Date | End date | Ship Date | Notes |
Started | 12 | HDMI Cables | 100 | 0 | 100 | 150 | 50 | 10/15/21 | 10/20/21 | ||
In Progress | 13 | HDMI Cables | 100 | 0 | 100 | 125 | 25 | 10/16/21 | 10/20/21 | ||
Done | 14 | HDMI Cables | 100 | 0 | 100 | 100 | 0 | 10/17/21 | 10/18/21 | 10/20/21 |
SUMMARY
Dynamics 365 advanced delivery route planning employs machine learning algorithms that can learn about delivery operations by evaluating historical data, such as improving delivery time estimations and enhancing overall efficiency and customer experience.
Finally, with Dynamics 365, users can improve delivery efficiency and fleet productivity, lower operational and transportation costs, and meet rising consumer demands.
Creating Delivery Schedules in Dynamics 365
This method demonstrates how to build a sales order delivery schedule. When a quantity on an order or a quotation is required to deliver subsequent shipments, a delivery schedule is employed. You can use the example data company USMF or your own data to execute this method.
Step 1
Go to All sales orders.
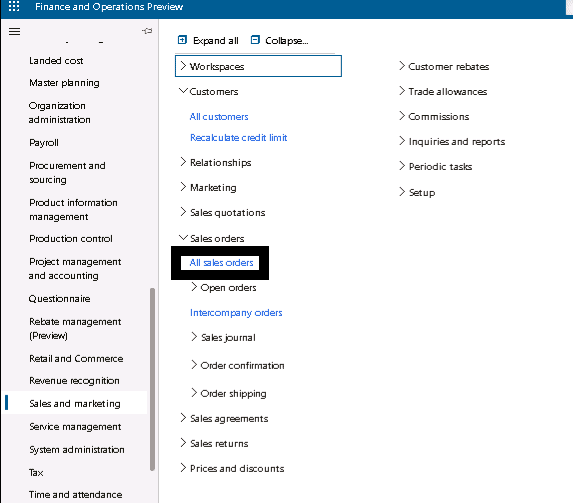
Step 2
Click New.
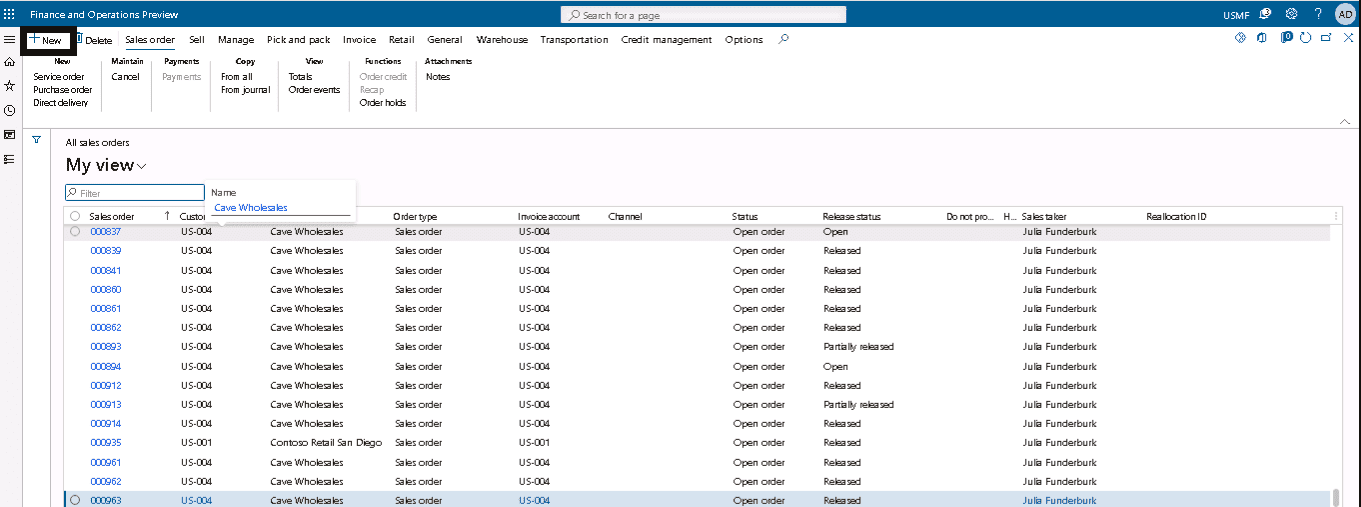
Step 3
In the Customer account field, enter or select a value.
Step 4
Click OK.
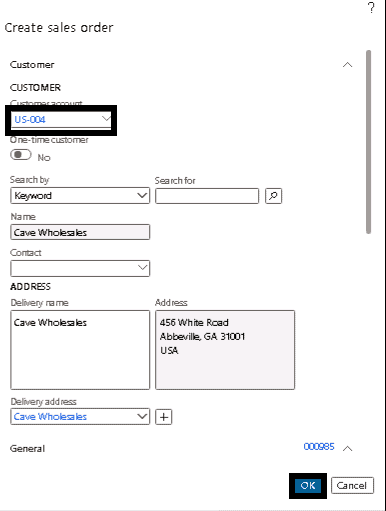
Step 5
In the Item number field, enter or select a value.
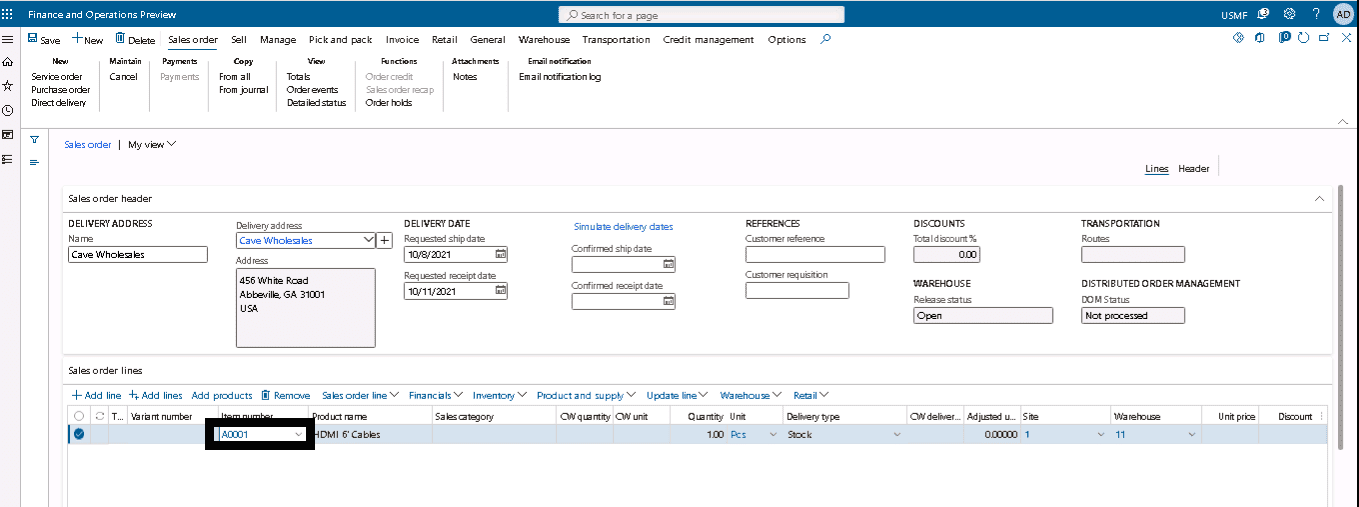
Step 6
In the Quantity field, enter a number that is bigger than 1.
Step 7
Click Sales order line.
Step 8
Click Delivery schedule.
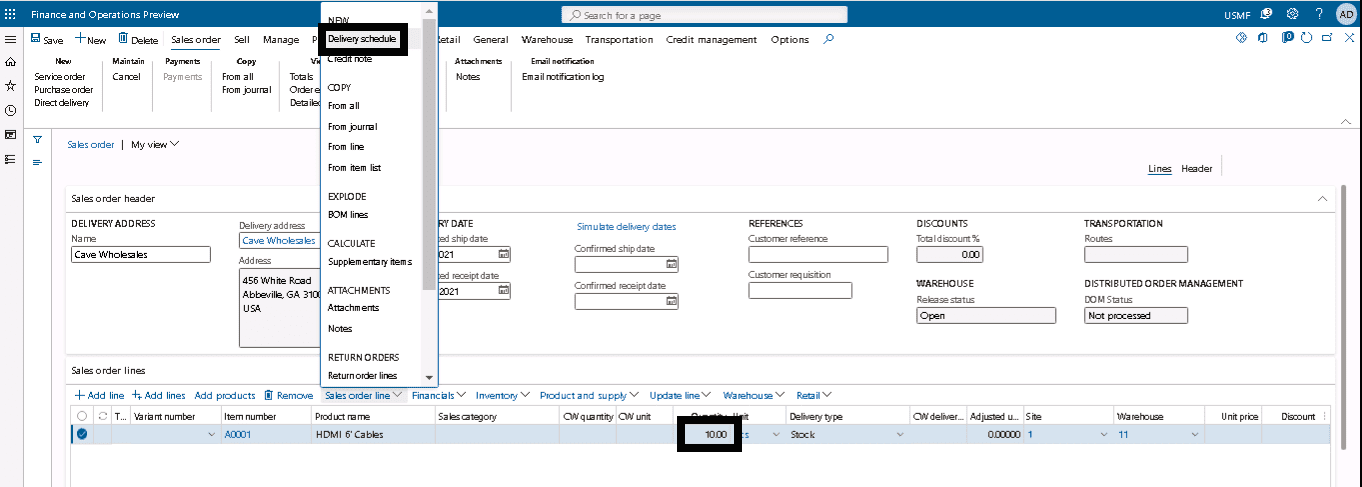
- The Delivery schedule page is the place where you can specify the number of shipments in which the total quantity of the order line will be delivered to the customer.
- By default, the system copies the original sales line’s total quantity and other delivery details into the first delivery schedule line. We’ll create a schedule for two shipments in this example, with the second shipment’s date offset by a week from the first one.
Step 9
In the Quantity field, enter a number that is part of the total quantity.
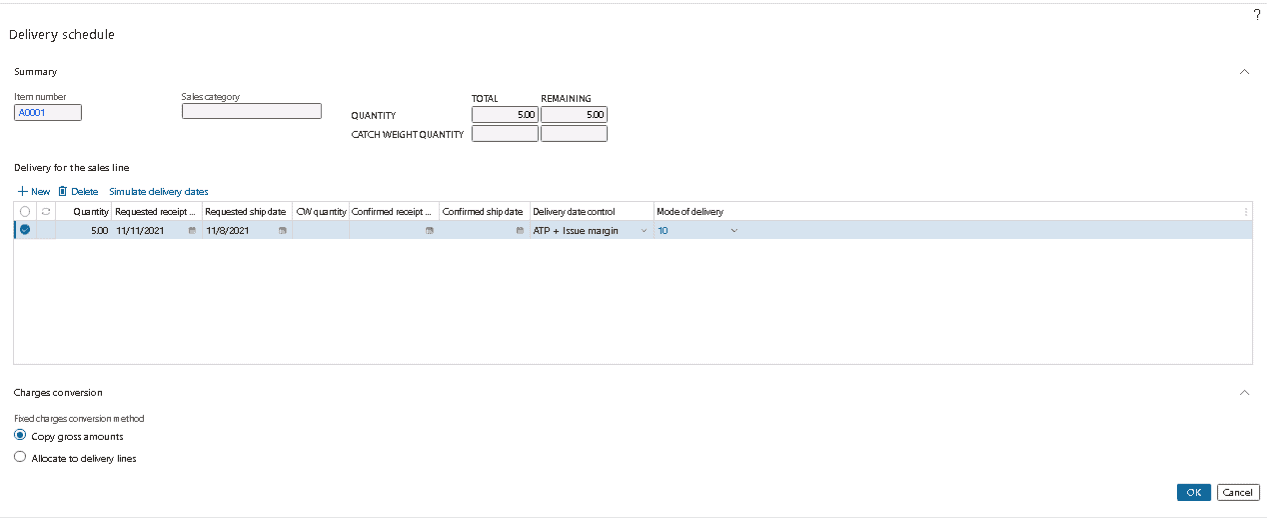
Step 10
Click New in the Quantity field, enter the remaining quantity.
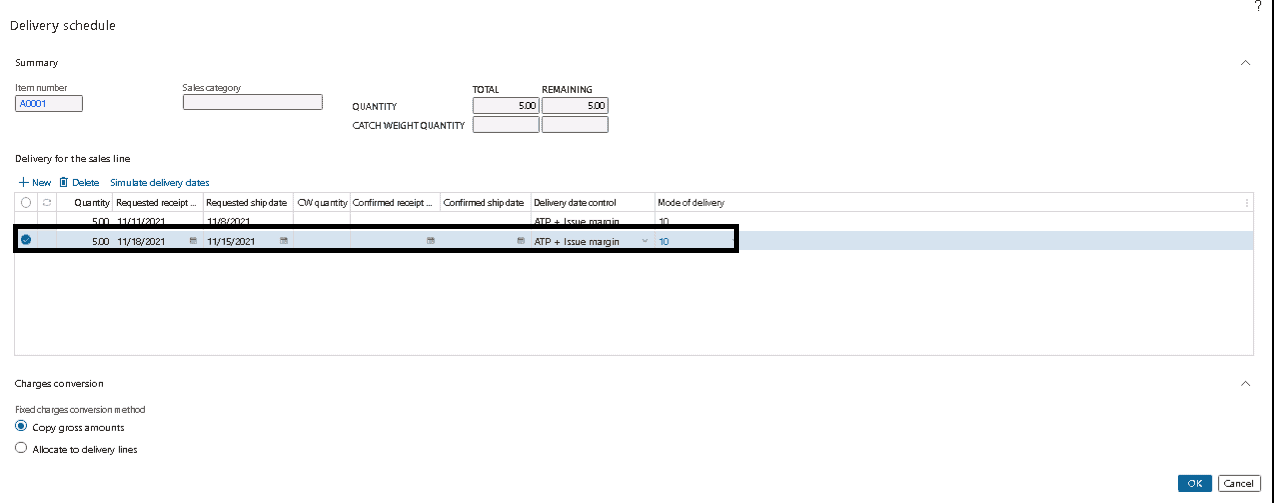
Step 11
In the Requested ship date field, enter a date that is one week ahead of the date of the first delivery line.
Step 12
Click OK.
Step 13
On the Action Pane, click Pick and pack.
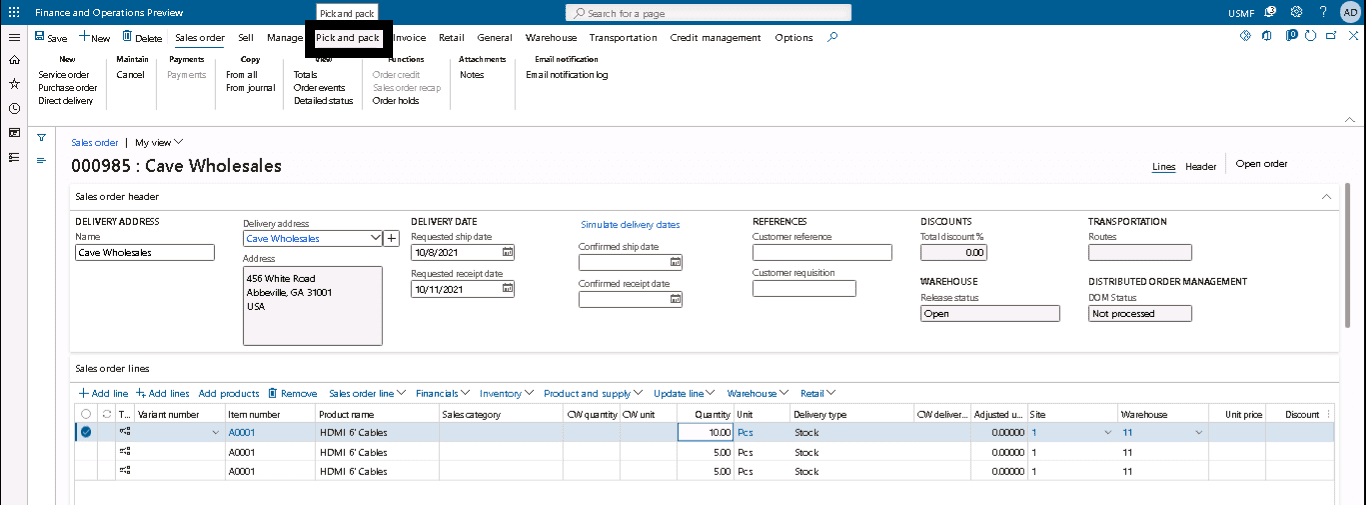
Step 14
Click Post packing slip.
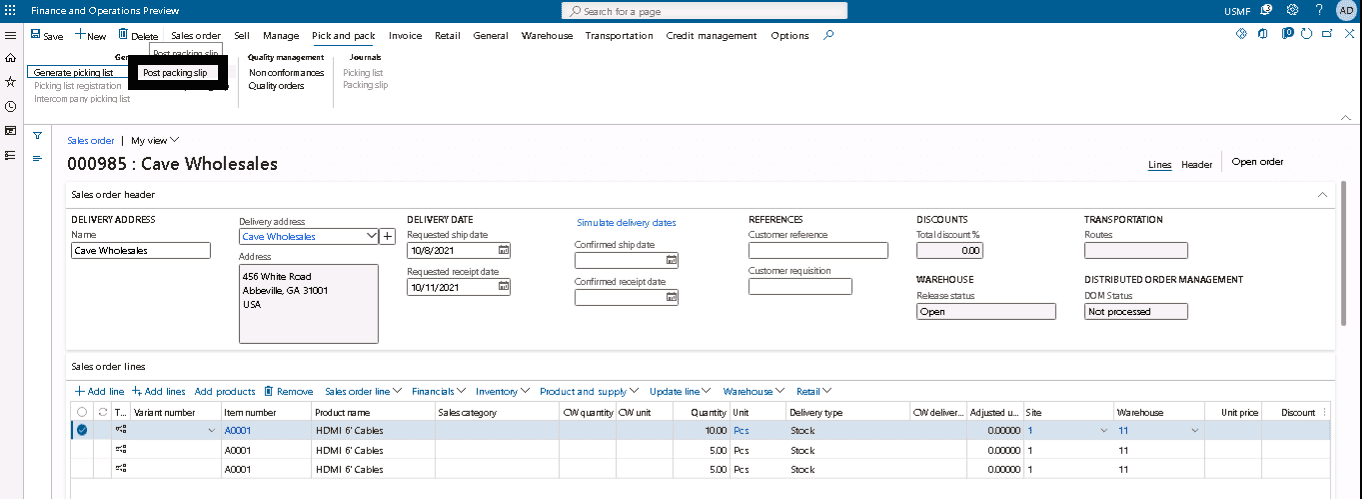
Step 15
Expand the Parameters section.
Step 16
In the Quantity field, select ‘All.’
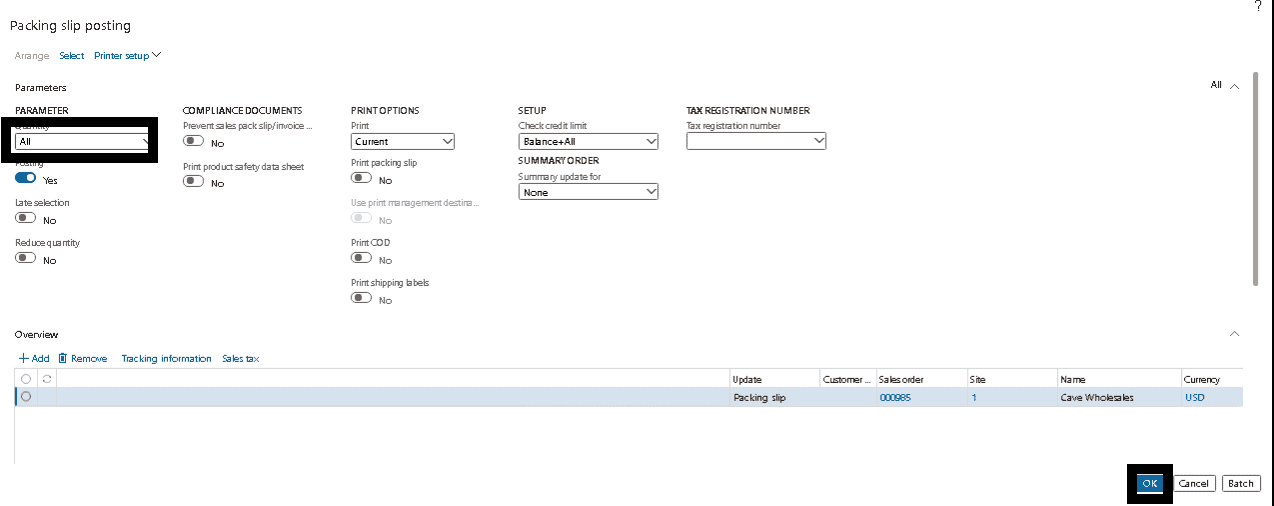
- Note that the packing slip will be created for the two delivery schedule lines and not the original order line.
Step 17
Select Yes in the Print packing slip field.
Step 18
Click OK.
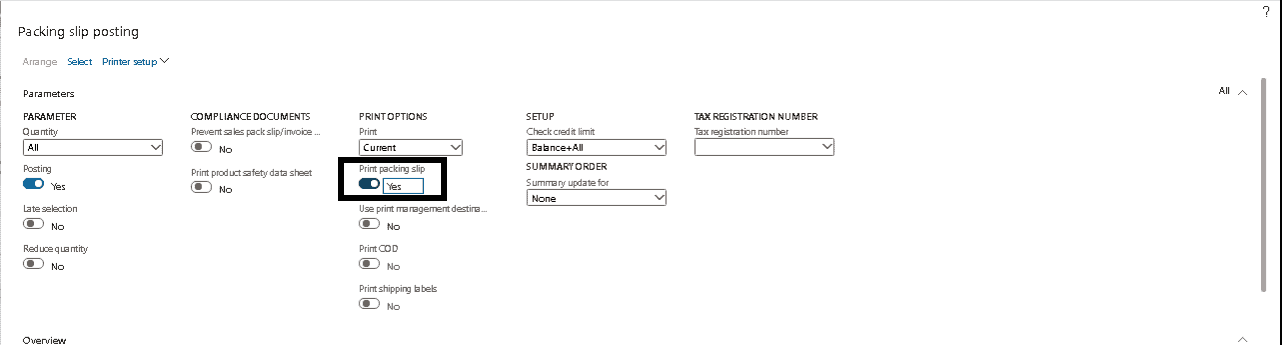
Step 19
Click Yes.
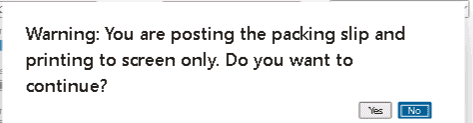
Step 20
Close the page.
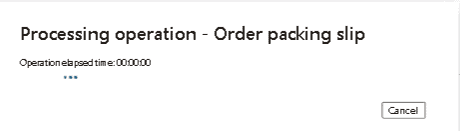
SUMMARY
The above procedure of creating scheduled deliveries starts with creating a new sales order and extends to entering or selecting required values, with delivery scheduled dates and times. Further, the user proceeds to post the packing slip and expanding parameters to get the printed packing slip. This whole procedure signifies that your delivery will get in the scheduled time without any interruptions.
Scheduled Deliveries in a Nutshell
Scheduled deliveries determine which orders will get delivered first and what routes they will opt for while doing so. In the introduction of this blog, we discussed how users could perform delivery schedules for each order line. However, this being a tedious and slow process, we turned towards Dynamics 365 scheduled deliveries for handling multiple deliveries and minimizing error occurrence.
Evidently, an optimized delivery schedule is a process of evaluating the potential combination of options and restrains to get on schedule, making the most efficient use of resources. In today’s competent world, scheduling deliveries involves modern optimizing techniques due to their ability to process more extensively and swiftly determine the most accurate and successful delivery schedule. Dynamics 365’s delivery schedule includes optimized algorithms and complex techniques employed by AI and machine learning to get you the results your business requires.
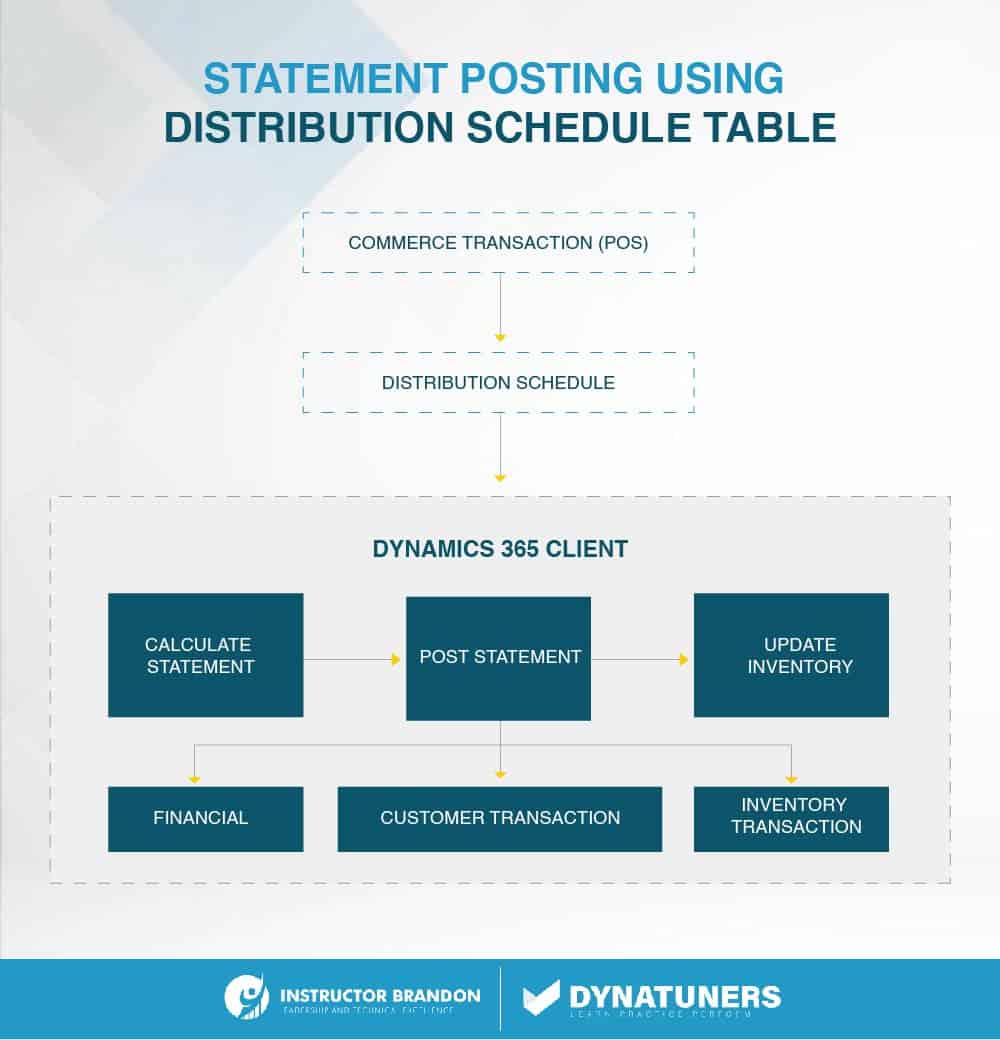
SUMMARY
Delivery schedules in Dynamics 365 has a very broad functionality. However, we have explained how they work and carry out ease in transportation and warehouse management.
At Instructor Brandon | Dynatuners, we always seek innovative methods to improve your competitiveness and suit your Microsoft Dynamics 365 requirements. Our offerings are founded on defined procedures, industry experience, and product understanding. If you’re interested in consulting with our specialists on how we can help you manage your cashflows perfectly, don’t hesitate to Contact Us.
[sc_fs_multi_faq headline-0=”h2″ question-0=”What is difference between contract and scheduling agreement?” answer-0=”A contract is a type of procurement plan by which the release orders (releases) can be issued for materials or services agreed as necessary for a certain period overall. But Scheduling agreement is a form of procurement plan under which the materials are purchased on dates within a certain time. ” image-0=”” headline-1=”h2″ question-1=”What is SAP delivery schedule?” answer-1=”Document sent by Electronic Data Interchange (EDI) or fax to the component supplier to release a quantity of the material or materials outlined in the scheduling agreement. The delivery schedule contains information on delivery quantities and dates. ” image-1=”” headline-2=”h2″ question-2=”Does in transit mean it will be delivered today?” answer-2=”Your shipment is moving within the UPS network and should be delivered on the scheduled delivery date. A shipment can remain in this status until it is delivered.” image-2=”” count=”3″ html=”true” css_class=””]